The client has discovered they have a need for a product or service in their laboratory setting that requires expertise. They may not be familiar with what they need and hence need professional advise. The client contacts Walton Plastics Engineering for their professional service.
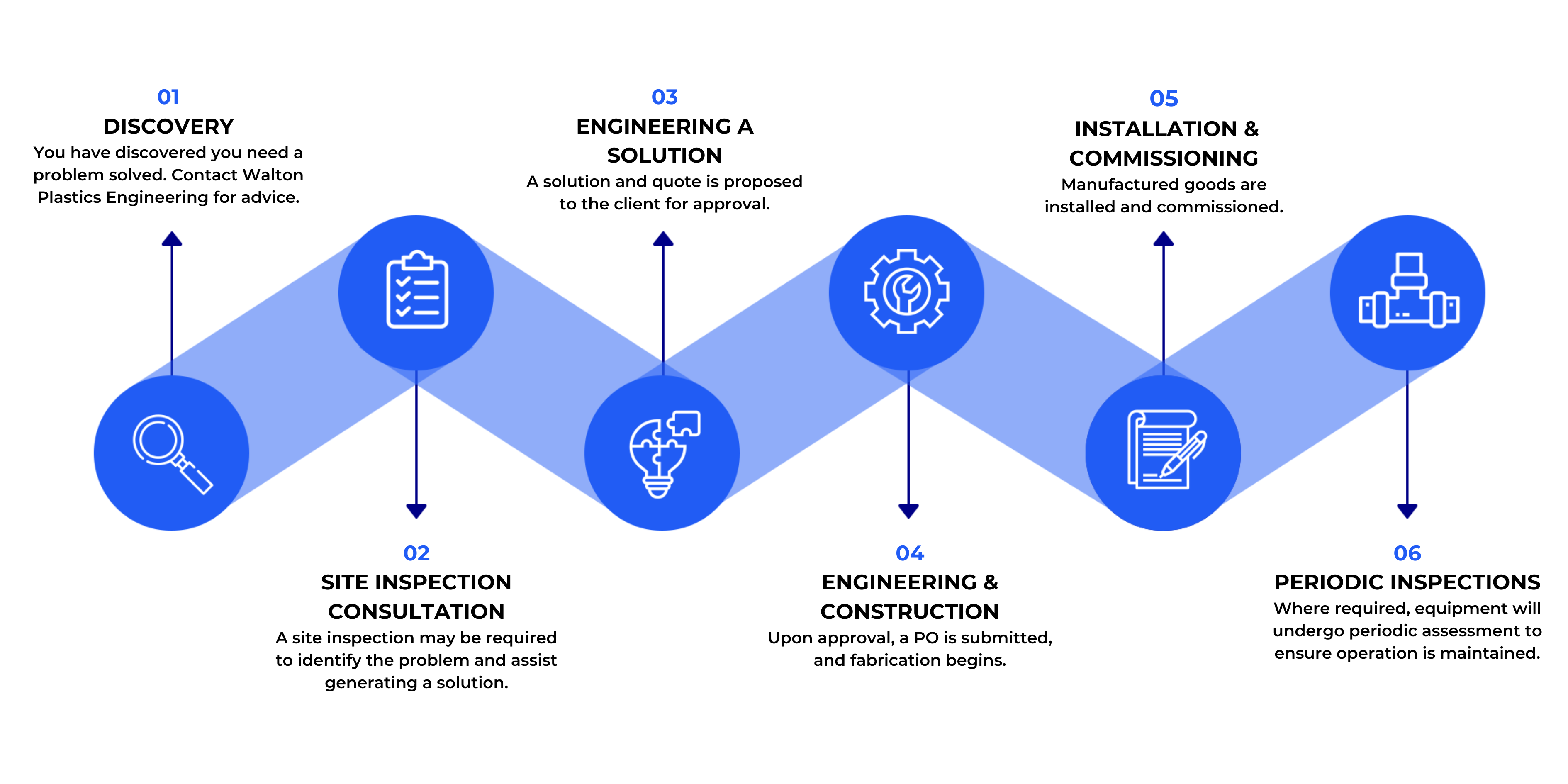
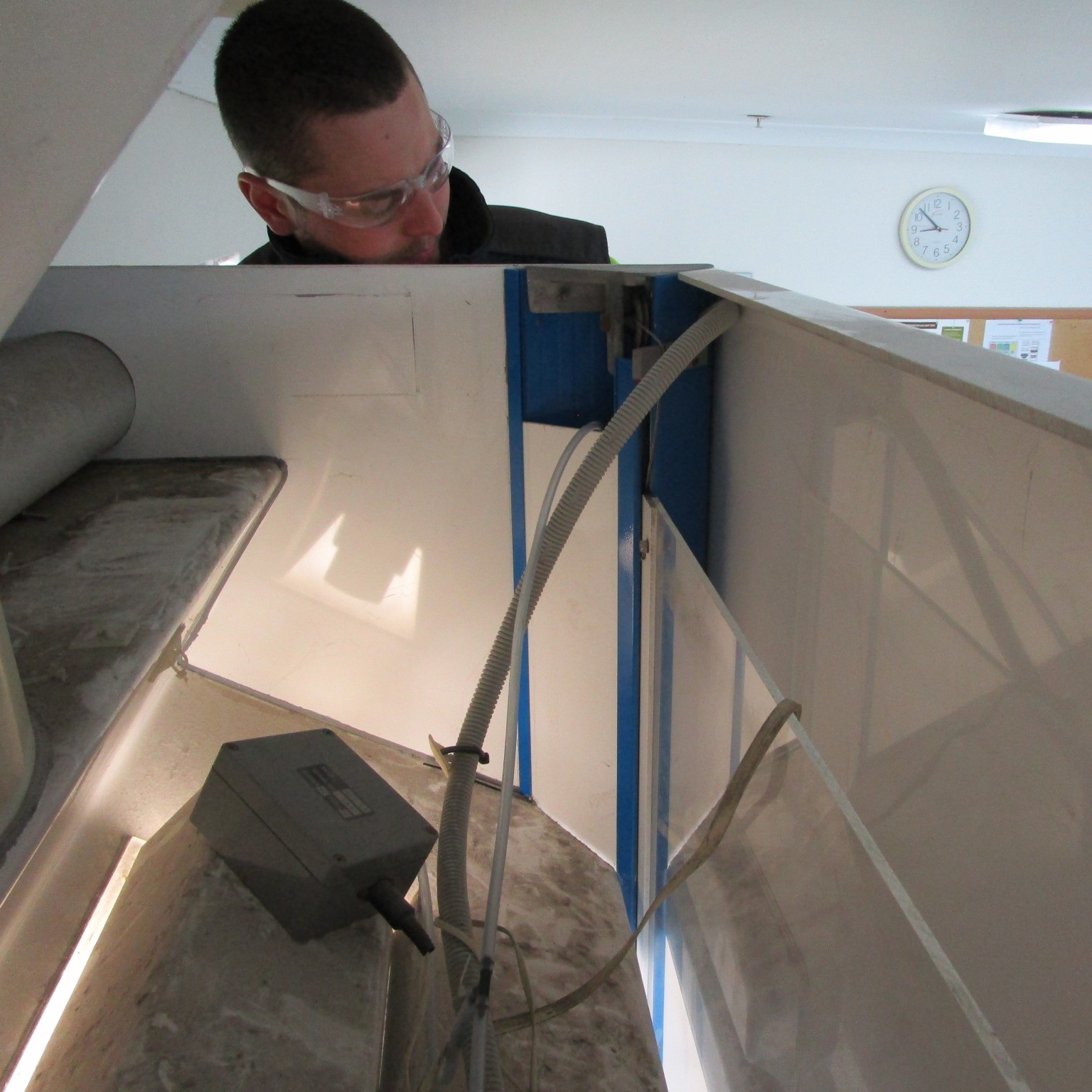
01 Discovery
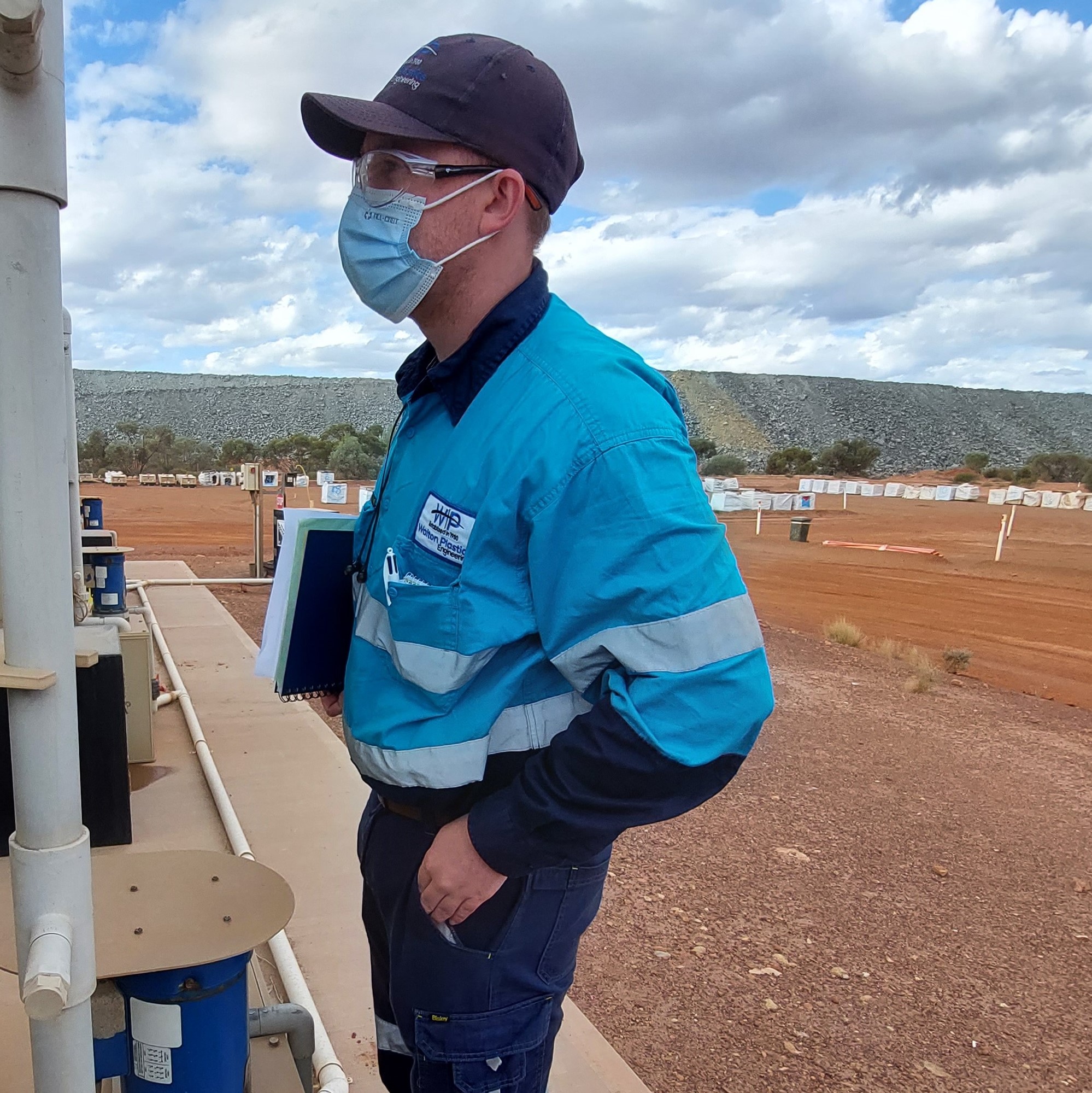
02 Site Inspection Consultation
An enquiry is raised which leads to a site inspection to speak to the client, understand the problem and inspect the site. The Walton Plastics Engineer will ask various questions, take measurements and perform calculations to best suit the problem. All the necessary information to engineer a solution will be generated at this stage.
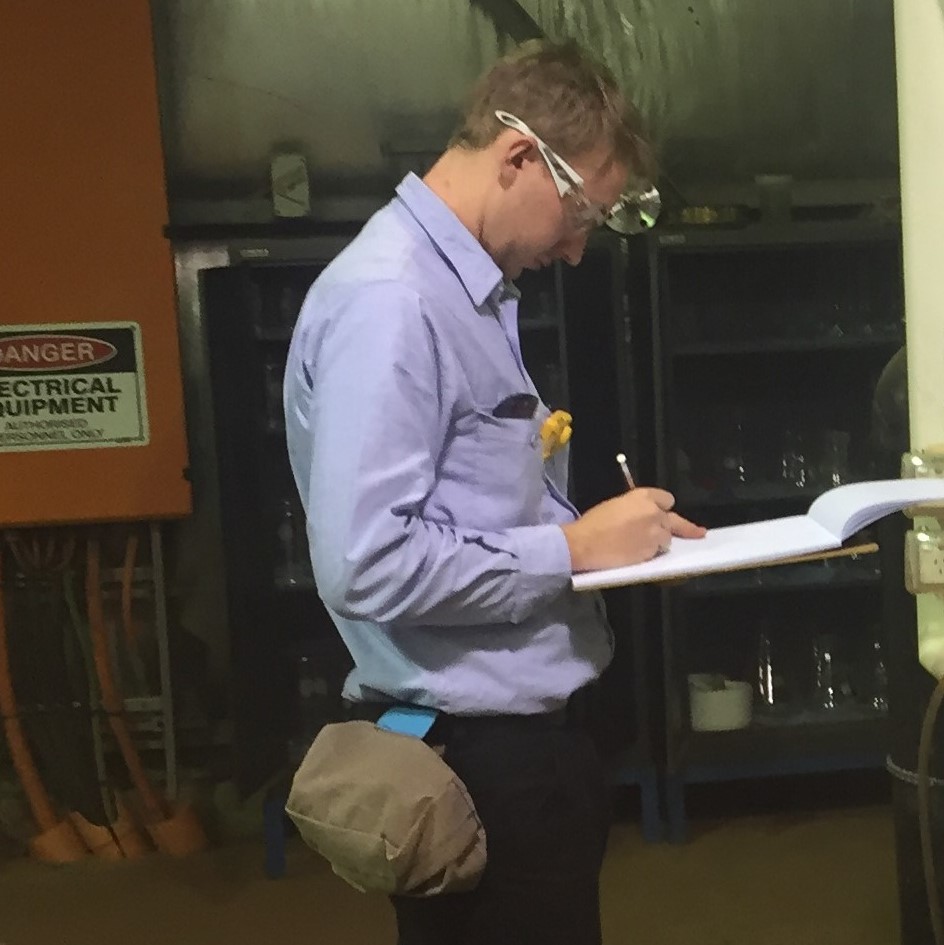
03 Engineering a Solution
After the site inspection where all necessary information has been gathered, the engineer will quote a solution for the clients approval. Typically there will be some further collaboration where drawings, sketches and calculations will be submitted to ensure both the client and the engineer understand the scope. Typically this stage takes some time.
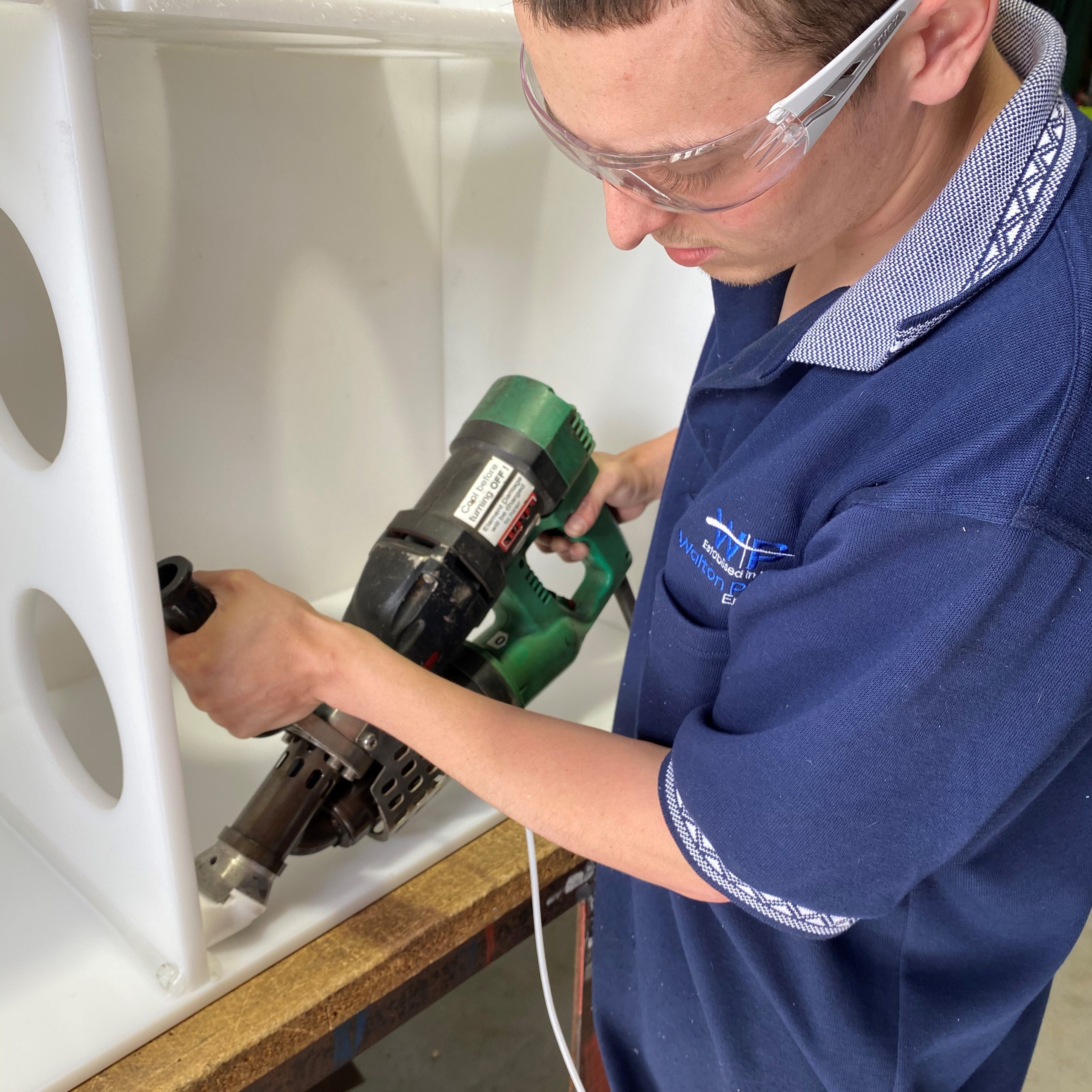
04 Engineering & Construction
Once the solution has been submitted and approved with PO sent, fabrication of the product will begin. This will also include planning for delivery and installation which may entail additional site inspections and collaboration with external trades.
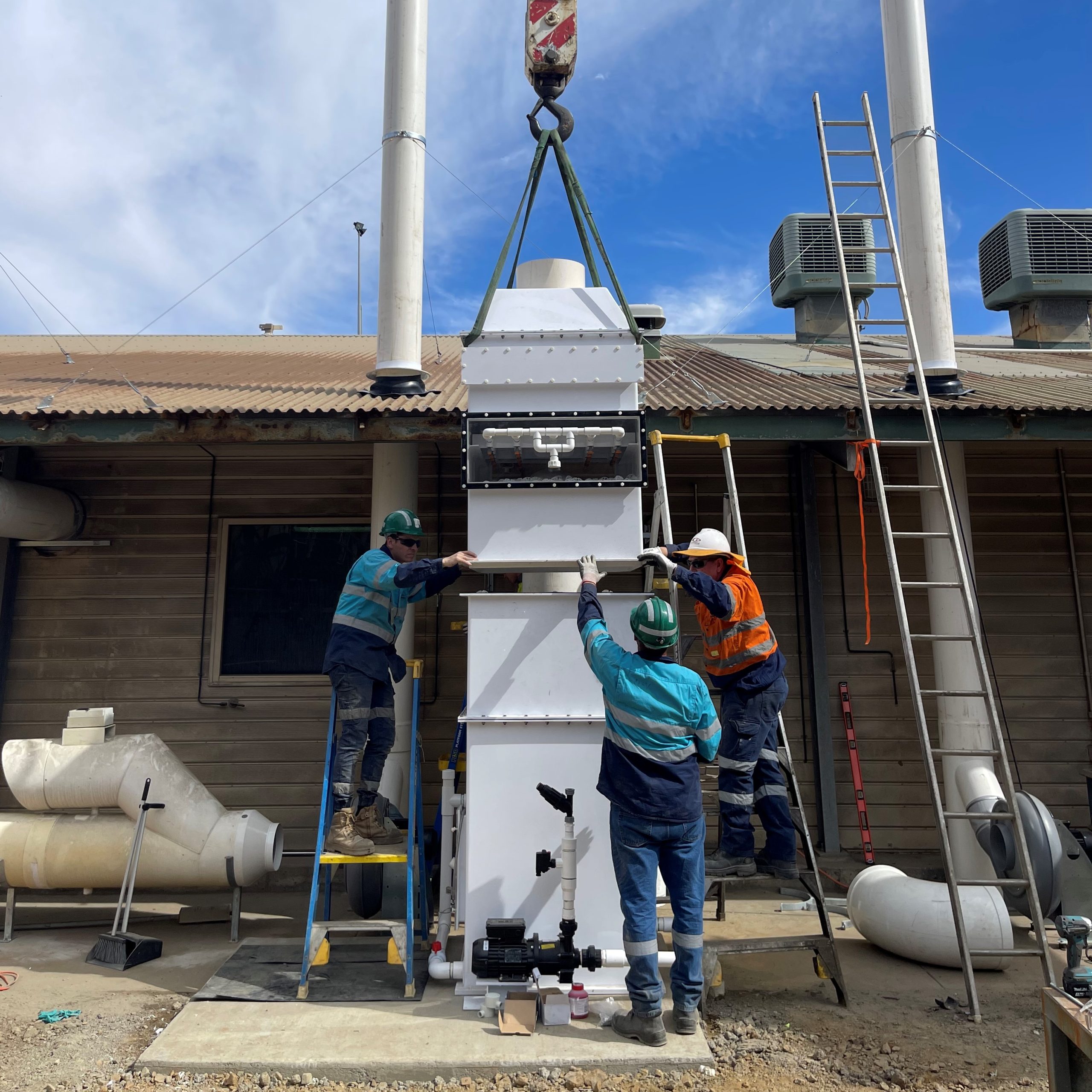
05 Installation and Commissioning
The fabricated products are now ready for installation. Products are delivered to site and installed into position. Products are tested against standards and compliance to ensure operating on site as intended. Hand over of products after commissioning will occur for working order.
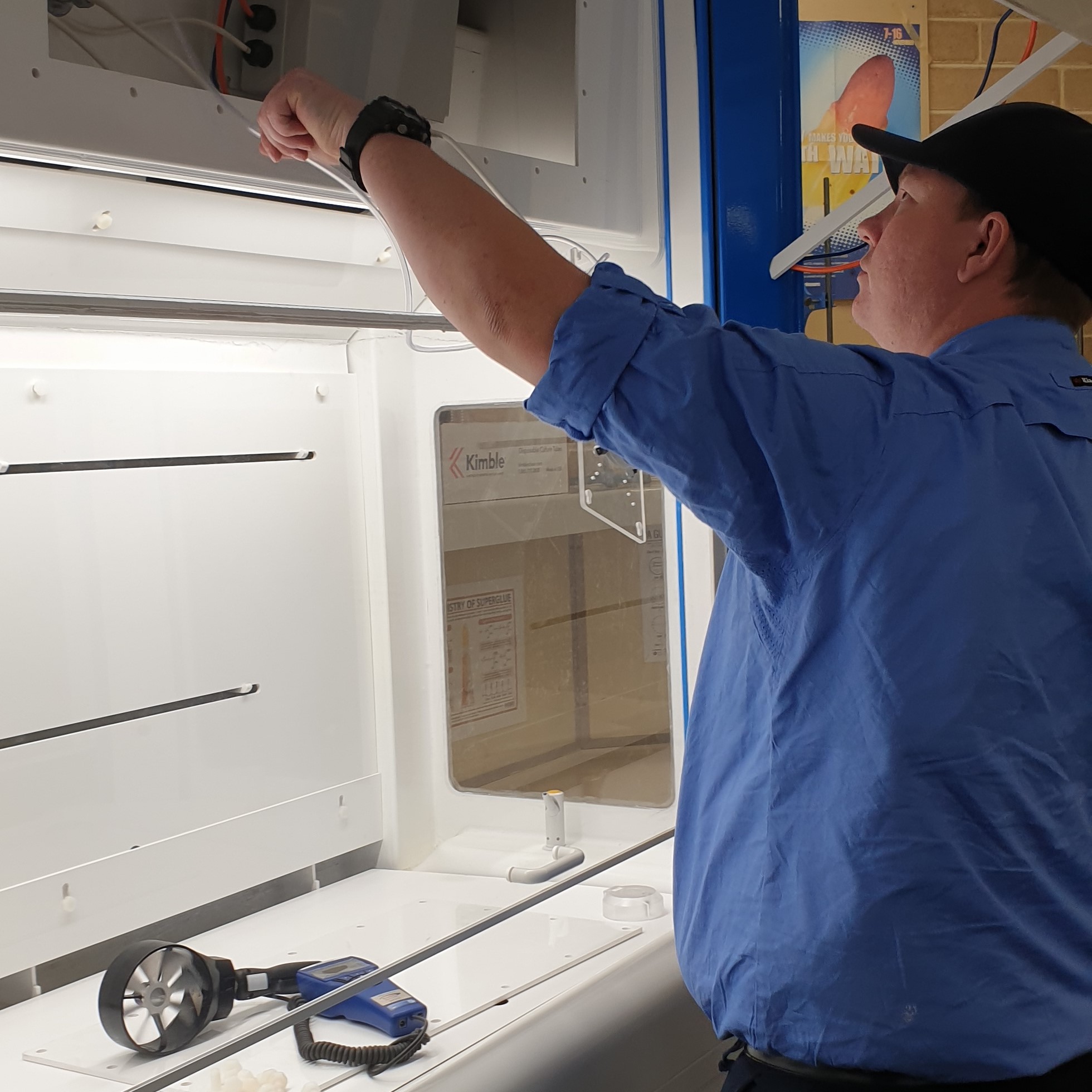
06 Periodic Performance Testing
When required, products are tested against standards and compliance to ensure they are operating as intended. This may include a series of compliance checks and tests where any service and maintenance items are noted and scheduled to maintain product longevity.